The Top Factors to Consider When Choosing Aluminum Framing for Your Project
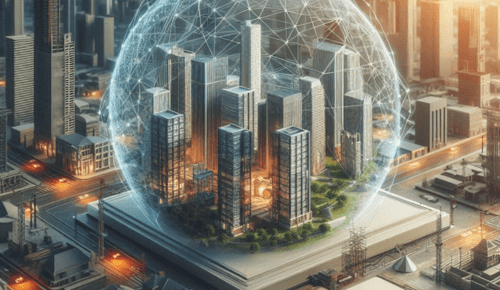
Every project comes with its own set of challenges, and selecting the right aluminum framing can make all the difference in durability, efficiency, and long-term performance. The right choice depends on several key factors, from structural strength to environmental exposure. Understanding these considerations will help ensure the aluminum framing system meets the exact needs of the project.
Specific Project Demands Determine Ideal Aluminum Profile Strength
Not all aluminum framing is created equal, and the specific needs of a project dictate the necessary profile strength. Structural applications, such as load-bearing frameworks or heavy-duty machinery supports, require aluminum profiles with higher tensile strength. In contrast, lightweight frames for partitions or decorative structures can utilize thinner-walled aluminum extrusions without sacrificing stability.
Engineers and designers often assess factors such as weight distribution, expected stress points, and overall load requirements before selecting an aluminum framing system. Choosing the wrong profile strength can lead to structural failure or unnecessary material costs. The right balance between strength and weight ensures the frame is both efficient and cost-effective while maintaining long-term durability.
Environmental Conditions Influence Aluminum Frame Selection
Outdoor installations and industrial environments expose aluminum framing to different elements that can impact its performance over time. In humid or coastal areas, corrosion resistance becomes a top priority. While aluminum naturally resists rust, additional protective coatings or anodization can enhance its ability to withstand moisture and salt exposure.
For projects located in high-temperature settings, thermal expansion should also be considered. Some aluminum alloys expand more than others, affecting connections and overall stability. Industrial environments may introduce chemical exposure, requiring aluminum profiles with specific finishes to prevent degradation. Factoring in these environmental conditions ensures the longevity and reliability of the framing system.
Customization Options Matching Your Project’s Precise Dimensions
Standard aluminum framing profiles may not always fit the unique specifications of a project. Customization options allow engineers and designers to modify dimensions, hole placements, and connection points to achieve a precise fit. This level of flexibility ensures the framing integrates seamlessly with the overall design.
For complex builds, custom machining or modular aluminum profiles can simplify assembly without sacrificing structural integrity. The ability to tailor aluminum framing to exact measurements also reduces material waste and additional labor costs. Whether it’s a specialized industrial framework or a unique architectural design, customization ensures efficiency and precision.
Speed of Assembly Dictates Framing System Preferences
Efficiency in construction and assembly is a major factor when selecting aluminum framing. Some framing systems use pre-drilled holes, modular connectors, or T-slot designs that make installation faster and easier. These features eliminate the need for welding or extensive machining, allowing teams to complete projects in less time.
For temporary structures or frequently modified setups, quick-assembly aluminum framing provides the flexibility to reconfigure layouts without extensive downtime. Time-sensitive projects benefit from aluminum framing systems designed for rapid installation, reducing labor costs and keeping timelines on track. Selecting the right framing system streamlines assembly and ensures a smoother construction process.
Maintenance Requirements Impact Long-Term Aluminum Choices
Low-maintenance materials save time and money over the lifespan of a project. Aluminum framing is already known for its resistance to rust and corrosion, but certain finishes and coatings can further extend its durability. Anodized or powder-coated aluminum resists scratches, fading, and chemical exposure, making it ideal for high-traffic or industrial environments.
Regular maintenance considerations include ease of cleaning, resistance to dirt buildup, and the ability to withstand physical impact. Some aluminum profiles are designed with smooth, non-porous surfaces that prevent dust and debris accumulation, reducing cleaning time. By selecting aluminum framing with the right finish and structural properties, long-term upkeep becomes effortless.
Load-Bearing Capacity Critical to Framing Profile Decisions
Understanding the weight a structure must support is essential when selecting aluminum framing. Load-bearing requirements influence the thickness, shape, and alloy composition of the aluminum profiles used in construction. Heavier loads demand reinforced or thicker-walled profiles, while lightweight applications benefit from slim yet sturdy extrusions.
In structural engineering, weight distribution and connection strength play a significant role in the overall stability of an aluminum frame. If the framing system must support dynamic loads, such as moving machinery or vibrating equipment, additional reinforcements may be necessary. Choosing aluminum framing with the appropriate load-bearing capacity ensures safety, performance, and longevity in any project.
Leave a Reply
You must be logged in to post a comment.
Leave a Comment